The idea of tying something up in a bow is an intriguing concept. It’s one that alludes to a sense of accomplishment, of finality, of conclusion. When it comes to our three larger-than-life Fern Floor ribbons, however, finite is not the concept we’re going for. While the multi-layered, multi-month, multi-person process of designing and creating the ribbons is in fact complete—and these sculptural ribbons have now found their Fern Floor home—the effect we’d like them to have is anything but finite. With their soft to energetic lines, and their rhythm and playfulness as they unravel and tumble along, the ribbons are meant to tell a different story from every different angle, and to every guest who views them. Part of their story is how they were made, from conceptualization to their “finishing” touches … and that’s a story I find to be a true page-turner.
The sheer size of these three wooden ribbons—totaling no less than 350 total feet and made up of 50 individual ribbon modules all joined together—is meant to play up a spirit of fun and imagination and engage the viewer in a sense of wonderment. The ribbons were designed to flow throughout the space, bringing a sense of fluidity and motion as they skim the Fern Floor surface.
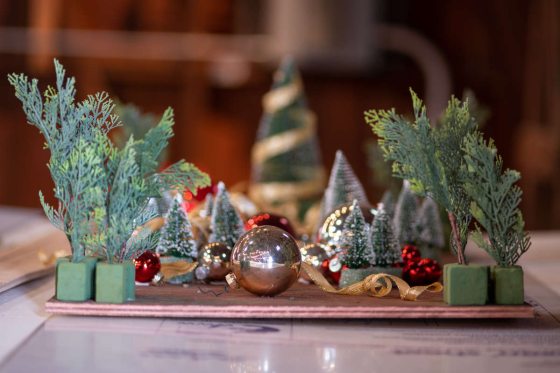
The initial concept of the ribbons started with a scale model. We knew we wanted the ribbons to twist, turn, and interact with the trees and large-scale ornaments that would also be on the floor, so all the elements would work together, appear fluid, and provide a sense of whimsy no matter the angle from which they’re viewed.
While designing the overall look, we thought about the overall height of the ribbons, how many pieces we wanted to create, and how many curves we wanted the ribbons to follow … which all factored into how many molds we needed to create. In the end, we ran nine different molds of varying shapes. Some took more of a trajectory type line, while others ran a simple curve, and others took complex twists to loops.
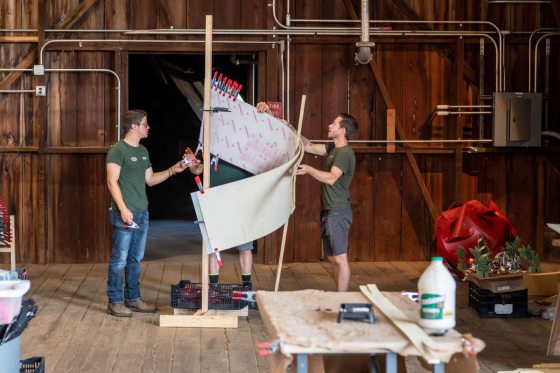
Once we had fabricated the molds, it was time to bring the wood into play. In order to achieve the ribbons’ twists and turns, we used two types of bending wood: an Italian bending poplar for the exterior of the ribbon and for the interior a bending mahogany. Both allowed for flexibility and malleability. These types of wood are typically used by furniture makers; their grain runs in the same direction as opposed to regular plywood, in which the grain is staggered, thereby making the wood very rigid.
To construct the 50 individual modules of ribbon, we bent the first layer of wood around the mold on a scaffolding piece, complete with pivoting arms that allowed us to twist and turn the material.
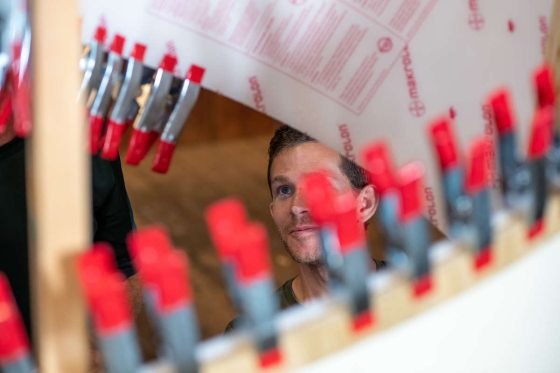
We glued inside ribs along the interior of the curved ribbon, and then attached those ribs to the outer wooden ribbon layer. We constantly sanded and evened out the edges along the way. After all of the layers of wood were bent around the plastic for each section, the plastic was then removed. Once we had our individual modules ready to go, it was time to connect them and create three distinct ribbons of varying twists and turns. We assembled the ribbons together piece by piece, starting from the ends of the ribbon that would be closest to the towering Exhibition Hall stage tree.
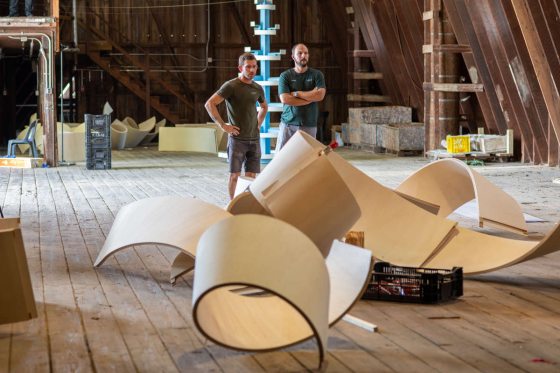
We first joined the modules together in a mockup capacity to figure out the flow of each ribbon, temporarily joining them together with screws. Fitting them together was quite a process, but a really fun experience. While fitting them together and figuring out the flow, we constantly had to find balance and harmony between each ribbon—and in the space as a whole—as the ribbon forms evolved. We assembled and arranged the pieces in a process that I created and termed as “entwine” while obtaining my Master of Fine Arts from the Herron School of Art and Design at Indiana University.
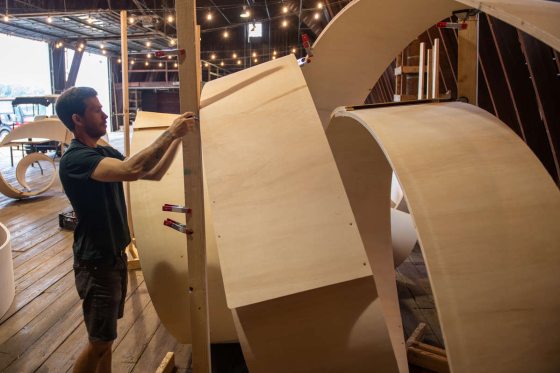
Once we were happy with the design, we took the connected pieces apart … yes, you read that right: we built the ribbons to then take them apart before permanently rebuilding them again.
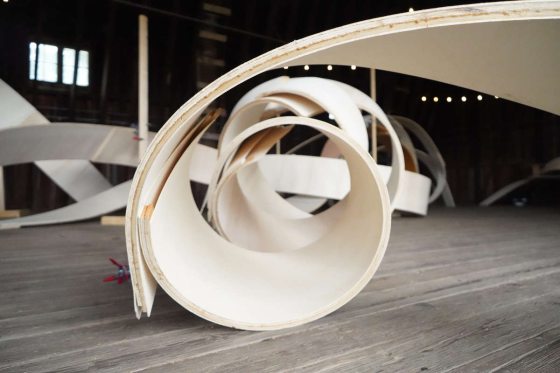
When it was time to permanently connect the modules in ribbon form, we locked them together via tongue and grove construction (which we had planned for by ending each piece with a tongue and groove), gluing and sanding the seams as we went. We used two thin ribs on the outer edge of the ribbon to allow from for the tongue and groove construction. We clamped temporary bridges on either end of the seams to allow for support while the glue dried. In total, the ribbon is made of four layers of wood that together make the ribbons strong, yet flexible.
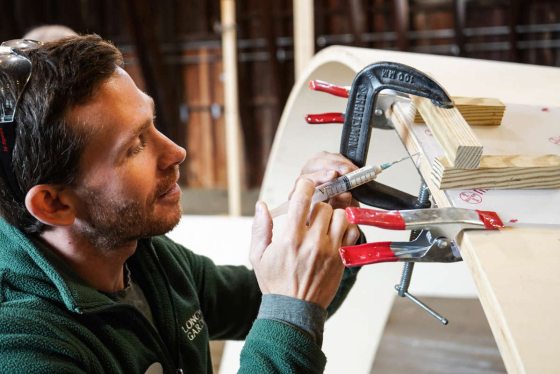
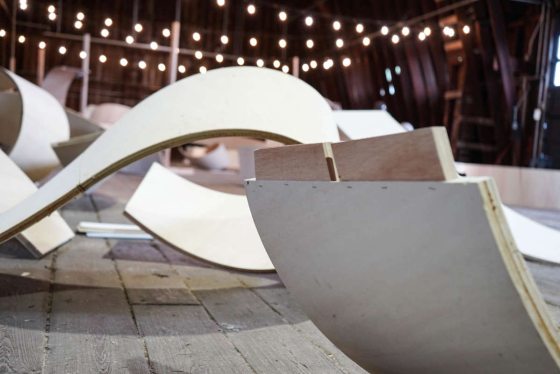
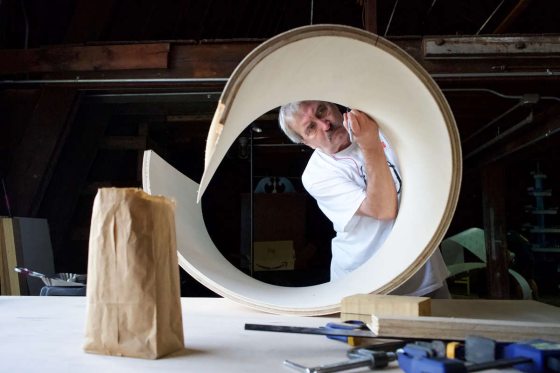
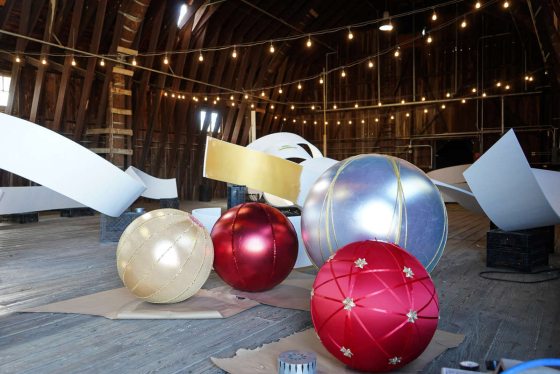
Before transporting the pieces to the Fern Floor for final assembly, we adhered shimmering, textural gold wallpaper on every square inch of the forms—through all of their twists and turns—to give the ribbons an engaging glimmer from every angle.
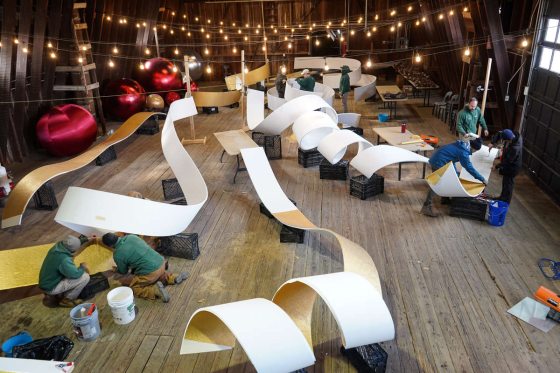
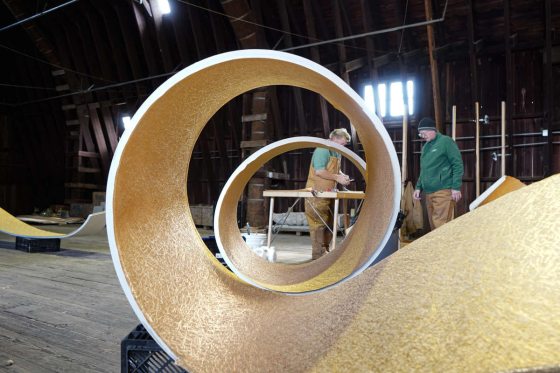
Using our permanent assembly process, we completed five spiraling pieces of gilded ribbon in the barn. We then transported those pieces from the barn to the Fern Floor, where we joined them together into three final ribbons during our final install … including a portion rising from the Fern Floor and wrapping around one of the surrounding columns.
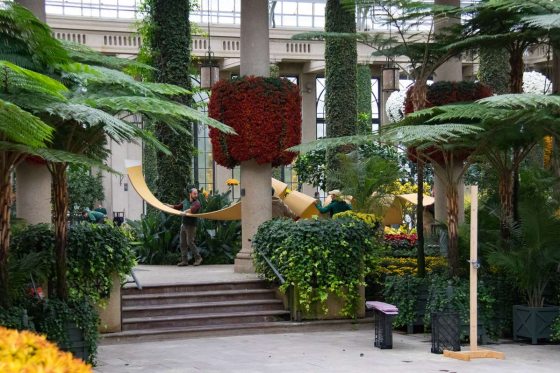
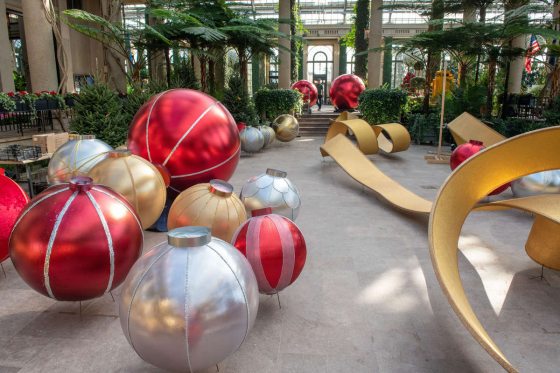
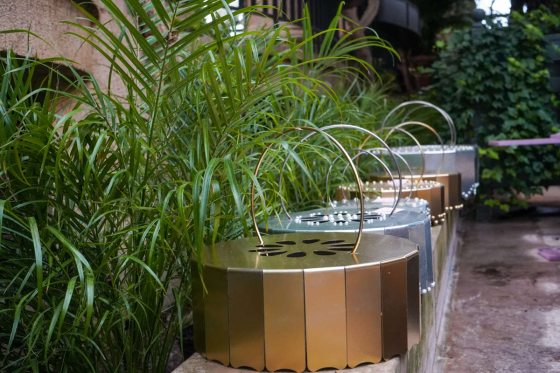
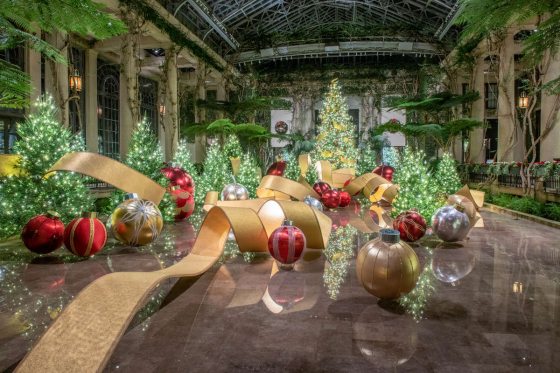
From conceptualization to final installation, our three Fern Floor ribbons are a beautiful representation of the many, many people who helped bring them to life. As an artist, I aspire to produce public sculpture that not only interacts with its space but also the people viewing it … so this experience creating the Fern Floor ribbons has brought my work as an artist and as a Longwood horticulture specialty grower full circle. It’s a very humbling, very inspiring experience to work with people so talented in their craft, and it speaks to me what A Longwood Christmas is all about … experiencing the magic of the season, together.